Gvtong Workshop
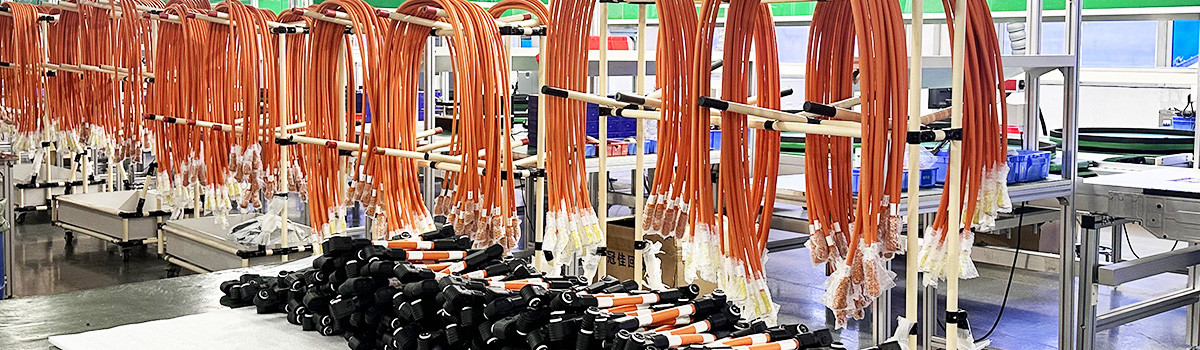
Shenzhen Gvtong Electronic Technology Co., Ltd. was established in 2010. It focuses on the design and manufacturing of connectors, precision injection molding, copper bus soft and hard connections, wire harness products, non-standard custom parts and other connection products. It is mainly used in automotive high and low voltage, charging and battery swapping. systems, as well as industrial control, chargers, energy storage, photovoltaics and other industries.
The company currently has more than 1,200 employees and covers an area of 55,000 square meters. It has established branches and production bases in Shenzhen, Huizhou, Suzhou, Anhui, Hefei, Fuyang and other places.Won the national high-tech enterprise, ISO9001, 14001, 13485, IATF16949 and other system certifications.
We continue to promote product innovation and have established a R&D team with doctors and graduate students as the backbone; we have established a complete quality management system and established a national CNAS laboratory to ensure product stability and promote product updates and iterations, which is the foundation of our foothold. , is also the driving force for our development.
With more than 10 years of industry experience and exploration, we have grasped the development trends of new energy and other industries, reduced costs, increased efficiency, and developed rapidly, and have become a trusted partner of customers.
Wiring Harness workshop
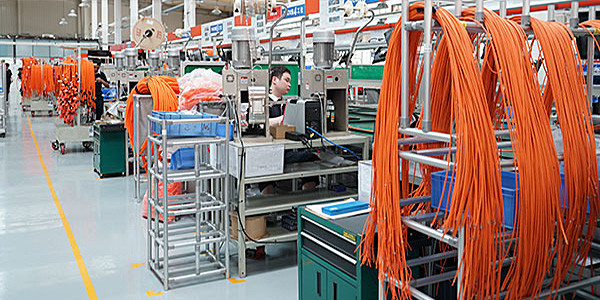
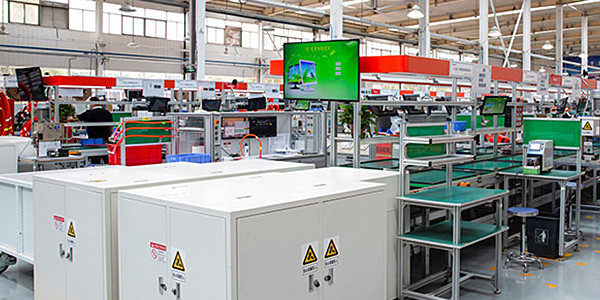

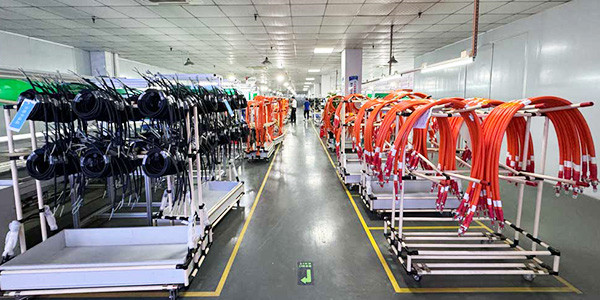
Stepping into Jvtong’s wiring harness workshop reveals a blend of meticulous craftsmanship and cutting-edge technology. Technicians work at organized stations, transforming detailed engineering designs into functional products. The process starts with cutting wires to exact specifications, followed by stripping insulation, attaching terminals through crimping, and bundling everything into a cohesive harness. Each step demands accuracy, as even a small error could disrupt a vehicle’s performance.
Quality control is a top priority in these workshops. Every harness is subjected to exhaustive testing—checking for electrical continuity, insulation integrity, and resilience under harsh conditions like heat or vibration. Many facilities now use automated testing equipment to boost efficiency and ensure compliance with strict automotive standards.
Innovation drives these workshops as much as precision does. Manufacturers are adopting lighter materials and developing high-voltage harnesses to meet the demands of electric vehicles. The push for sustainability and performance has also sparked advancements in data-transmitting capabilities, essential for today’s smart cars.
The workshop itself is engineered for success. Clean, well-lit spaces and ergonomic setups enhance productivity while strict safety measures protect workers handling electrical components. Looking ahead, these workshops must adapt to industry shifts by embracing automation and upskilling their teams. In doing so, they’ll continue to power the vehicles of tomorrow, one harness at a time.
Connector workshop
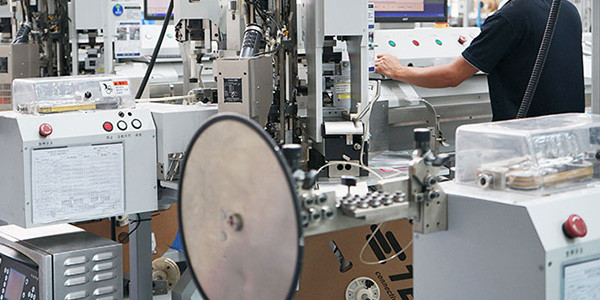
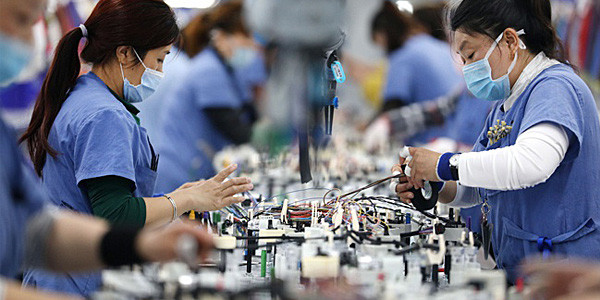
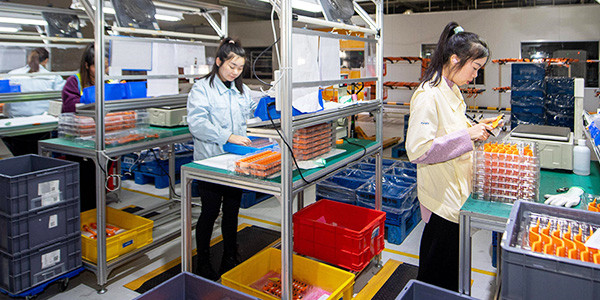
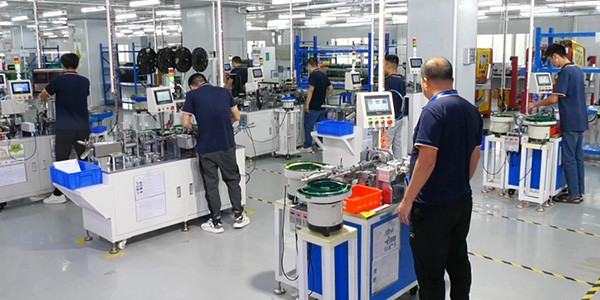
Jvtong High Voltage Connectors with Strict Quality Control
Our products are used extensively in the EV industry and have been tested according to international standards. We can also provide you with customized solutions that meet your specific requirements. With over 15 years’ experience in the field of high voltage connectors, we have built up a comprehensive range of solutions for safe power distribution and control in your electric vehicles (EV). We have cooperated with many well-known domestic and foreign partners.